Video: Suomen kirjallisuuden lyhyt historia @ Keski-Espoon kirjasto 2025
Kuinka terästeollisuus kehittyi sen juurista raudan valmistuksessa? Katsotaanpa katseet teräksen historiaa.
Raudan aika
Erittäin korkeissa lämpötiloissa rauta alkaa absorboida hiiltä, mikä alentaa metallin sulamispistettä ja johtaa valurautaan (2,5-5,5% hiiltä). Masuunien kehittyminen, jota kiinalaiset käyttivät ensimmäisen kerran 6. vuosisadalla eKr. Mutta laajemmin Euroopassa keskiajalla, kasvattivat valuraudan tuotantoa.
Sika-rauta
Sulatusrautaa, joka oli loppunut masuunissa ja jäähdytetty pääkanavalla ja vierekkäisissä muotteissa, kutsuttiin silikoniksi, koska suuret, keskus- ja vierekkäiset pienet valanteet muistuttivat emakoiden ja imeväisten porsaat.
Valurauta
Valurauta on vahva, mutta kärsii hiukkasista johtuen hauraudesta johtuen siitä, että se on vähemmän kuin ihanteellinen työskentelyyn ja muotoiluun. Koska metallurgistit saivat tietää, että raudan korkea hiilipitoisuus oli keskeinen osa haurauden ongelmaa, he kokeilivat uusia menetelmiä hiilipitoisuuden vähentämiseksi, jotta rauta toimisi toimivammaksi.
Taotut rautaa
1700-luvun loppupuolella rautavalmistajat oppivat muuttamaan valetun raudan raaka-aineeksi hiilipitoisuudeltaan takorautavalmisteita käyttäen vihreitä uuneja (Henry Cortin kehittämä 1784). Uunit kuumennettiin sulaa rautaa, jota oli sekoitettava puddlers käyttäen pitkät reiän muotoiset työkalut, jolloin happea yhdistettäisiin hiilen kanssa ja hitaasti poistettaisiin.
Kun hiilipitoisuus pienenee, raudan sulamispiste kasvaa, joten raudat massat agglomeroivat uunissa. Nämä massat poistettaisiin ja työstettäisiin kovakuorimyllyllä ennen kuin ne kääritään levyiksi tai kiskoiksi. Vuoteen 1860 mennessä Isossa-Britanniassa oli yli 3000 likaista uunia, mutta sen työ ja polttoaineen intensiteetti estivät prosessia.
Läpipainopakkaus
Yksi aikaisimmista teräksistä, läpipainopakkaus teräksestä, aloitti tuotannon Saksassa ja Englannissa 1700-luvulla, ja sitä tuotettiin lisäämällä hiilipitoisuutta sulassa raakaraudassa käyttäen prosessia tunnetaan nimellä sementointi. Tässä prosessissa takoraudoitetut palkit kerättiin jauhettua puuhiiltä kivi- laatikoihin ja kuumennettiin.
Noin viikon kuluttua rauta imeä hiilen hiilellä. Toistuva lämmitys jakaa hiilen tasaisemmin ja tuloksena jäähdytyksen jälkeen oli läpipainopakkaus. Suuremman hiilipitoisuuden läpipainopakkaus on paljon käyttökelpoisempi kuin raakarauta, jolloin se voidaan puristaa tai rullata.
Blister teräsvalmistus kehittyi 1740-luvulla, kun englantilainen kellokoneisto Benjamin Huntsman yrittäessä kehittää korkealaatuista terästä kellojousilleen havaitsi, että metalli voitaisiin sulattaa saviupokkailla ja puhdistaa erityisellä vuonnalla kuonan poistamiseksi, sementointiprosessi jäi jäljelle.Tuloksena oli upokkaat tai valurauta. Tuotantokustannusten takia sekä kuplapakkausta että valurautaa käytettiin vain erikoiskohteissa.
Tämän seurauksena valurautaa valmistettu valurauta pysyi ensisijaisena rakennetalana teollistuvassa Britanniassa suurimman osan 1800-luvulta.
Bessemer-prosessi ja nykyaikainen valmistus
Rautatiekuljetukset 1800-luvulla sekä Euroopassa että Amerikassa nostivat suuria paineita raudateollisuudelle, joka vielä kamppaili tehottomien tuotantoprosessien kanssa. Teräs oli edelleen epätodennäköistä rakennetallina ja tuotanto oli hidasta ja kallista. Tämä oli vasta vuoteen 1856, jolloin Henry Bessemer kehitti tehokkaamman tavan syöttää happea sulaan rautaan hiilipitoisuuden vähentämiseksi.
Nyt nimeltään Bessemer-prosessi, Bessemer suunnitteli päärynän muotoisen astian, johon viitattiin "muuntimella" - jossa rautaa voitaisiin lämmittää, kun happea voitaisiin puhaltaa sulan metallin läpi. Kun happi läpäisi sulan metallin, se reagoisi hiilen kanssa, vapautti hiilidioksidia ja tuotti puhtaampaa rautaa.
Prosessi oli nopea ja edullinen, poistamalla hiiltä ja piitä rautaa muutamassa minuutissa, mutta kärsinyt liian onnistuneesta.
Liiallinen hiili poistettiin ja lopputuotteessa oli liikaa happea. Bessemerin oli viime kädessä maksettava sijoittajat, kunnes hän löysi menetelmän hiilipitoisuuden lisäämiseksi ja poistaa ei-toivotun hapen.
Lähes samaan aikaan brittiläinen metallurgisti Robert Mushet osti ja alkoi kokeilla raudan, hiilen ja mangaanin yhdistelmää, joka tunnetaan nimellä spiegeleisen . Mangaanin tiedettiin poistavan happea sulasta raudasta ja spiegeleisen hiilipitoisuus, jos se lisätään oikeisiin määriin, antaisi ratkaisun Bessemerin ongelmiin. Bessemer alkoi lisätä sen muokkausprosessiin suurella menestyksellä.
Yksi ongelma säilyi. Bessemer ei ollut löytänyt keinoa poistaa lopputuotteesta peräisin olevaa fosforia - vahingollista epäpuhtautta, joka tekee terästä hauraaksi. Näin ollen vain Ruotsista ja Walesista peräisin olevia fosforittomia malmia voitaisiin käyttää.
Vuonna 1876 Welshman Sidney Gilchrist Thomas nousi liuokseen lisäämällä kemiallisesti perusvirtausmekkoni Bessemer-prosessiin. Kalkkikivi vei fosforin raakaraudasta kuonaan, jolloin ei-toivottu elementti poistettaisiin.
Tämä innovaatio tarkoitti, että lopulta rautamalmia kaikkialta maailmasta voitaisiin käyttää teräksen valmistamiseen. Ei ole yllättävää, että teräksen tuotantokustannukset laskivat merkittävästi. Teräsrautatien hinnat laskivat yli 80 prosenttia 1867-84 vuoteen 1884 uuden terästuotantotekniikan tuloksena, mikä käynnisti maailman terästeollisuuden kasvun.
Avoin keittoprosessi:
Saksalainen insinööri Karl Wilhelm Siemens kasvatti 1860-luvulla teräsvalmistusta luomalla avointa tulisijoitusta. Avotulen prosessi tuotti terästä raakaraudalta suurissa matalissa uuneissa.
Käyttämällä korkeita lämpötiloja liiallisen hiilen ja muiden epäpuhtauksien polttamiseksi prosessi perustui lämmitettyihin tiilikammioihin tulen alla.Regeneratiiviset uunit käyttivät myöhemmin pakokaasuja uunista korkeiden lämpötilojen ylläpitämiseksi alla olevissa tiilikammioissa.
Tämän menetelmän ansiosta oli mahdollista tuottaa paljon suurempia määriä (50-100 metristä tonnia voitaisiin tuottaa yhdessä uunissa), sulatetun teräksen määräaikaistestaus, jotta se voitaisiin tehdä erityisten eritelmien ja romumetallin käytön raaka-aineena. Vaikka prosessi itsessään oli paljon hitaampaa, vuoteen 1900 mennessä avoin tulisijan prosessi oli suurelta osin korvattu Bessemer-prosessilla.
Terästeollisuuden syntymä:
Teräsvalmistuksen vallankumous, joka tarjosi halvempaa ja korkealaatuisempaa materiaalia, tunnustettiin monien päivän liikemiehiksi sijoitusmahdollisuutena. 1800-luvun lopun kapitalistit, mukaan lukien Andrew Carnegie ja Charles Schwab, investoivat ja tekivät miljardeja (miljardeja Carnegien tapauksessa) terästeollisuudessa. Carnegien vuonna 1901 perustettu amerikkalainen Steel Corporation oli ensimmäinen lanseerattu yritys, joka oli yli miljardi dollaria.
Electric Arc Furnace Steelmaking:
Juuri vuosisadan vaihteessa tapahtui toinen kehitys, jolla olisi vahva vaikutus terästuotannon kehitykseen. Paul Heroultin valokaariuuni (EAF) on suunniteltu siirtämään sähkövirta ladattua materiaalia käyttäen, mikä johtaa eksotermiseen hapettumiseen ja lämpötiloihin, jotka ovat jopa 3272 ° F (1800 ° C) riittävät lämmittämään terästuotantoa.
Alunperin erikoisterästen erikoiskäyttöön tarkoitettujen terästuotteiden käyttö kasvoi, ja toisen maailmansodan aikana niitä käytettiin terässeosten valmistukseen. EAF: n tehtaiden perustamiseen liittyvät alhaiset investointikustannukset antavat heille mahdollisuuden kilpailla suurimpien yhdysvaltalaisten tuottajien kanssa, kuten US Steel Corp. ja Bethlehem Steel, erityisesti hiiliteräksissä tai pitkissä tuotteissa.
Koska EAF: t voivat tuottaa terästä 100%: sta romua tai kylmävalssausta, tarvitaan vähemmän energiaa tuotantoyksikköä kohden. Toisin kuin perus happea, toimintaa voidaan myös lopettaa ja aloittaa vähäiset kustannukset. Näistä syistä tuotanto on kasvanut jatkuvasti yli 50 vuoden ajan, ja sen osuus maailmanlaajuisesta terästuotannosta on noin 33 prosenttia.
Hapen valmistus:
Valtaosa globaalista terästuotannosta - noin 66 prosenttia - on nyt tuotettu perushapetiloissa. Menetelmä hapen erottamiseksi typestä teollisessa mittakaavassa 1960-luvulla mahdollisti huomattavat edistysaskeleet perustason hapen uuneissa.
Perus happiuunit happea happea suuriin määriin sulaa rautaa ja romumetallea ja voi suorittaa varauksen paljon nopeammin kuin avoimet tulisijamenetelmät. Suuret astiat, joissa on enintään 350 tonnia rautaa, voivat valmistaa teräsputken alle tunnin.
Hapankäsittelyn kustannustehokkuudet tekivät avoimien tulentakauppojen tehottomiksi, ja hapankäsittelyn tuloksena 1960-luvulla haponkestävä toiminta alkoi sulkeutua. Viimeinen avolouhintalaitos Yhdysvalloissa suljettiin vuonna 1992 ja Kiinassa vuonna 2001.
Lähteet:
Spoerl, Joseph S. Rauta- ja terästuotannon lyhyt historia . Saint Anselm College.
Saatavilla: // www. Anselm. edu / aloitussivu / dbanach / h-Carnegie-terästä. htm
Maailman teräsliitto. Verkkosivusto: www. steeluniversity. org
Street, Arthur. & Alexander, W. O. 1944. Metals in the Service of Man . 11. painos (1998).
Identiteettivarkauksen lyhyt historia
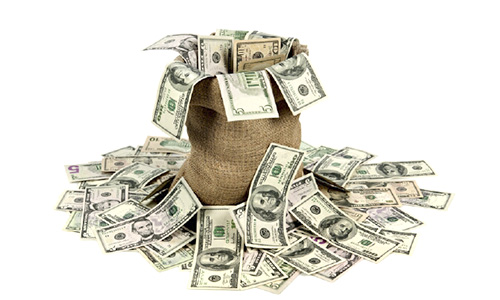
Identiteettivarkauden historia < < identiteettivarkauden historia juontaa jo jonkin aikaa; se jatkuu kehittämässä uutta tekniikkaa ja vaikuttaa monenlaisiin elämääsi
Lyhyt myynti ilman vaikeuksia - strateginen lyhyt myynti
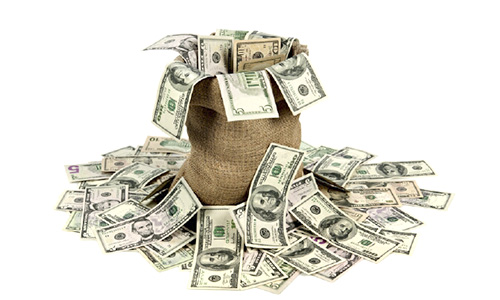
Strateginen lyhyt myynti ilman vaikeuksia on mahdollista tietyissä olosuhteissa. Kuinka tehdä mitään vaikeuksia lyhyt myynti.
Tyypin 304 ja 304L ruostumatonta terästä selitetty

Oppia eroa tyypin 304 ja 304L teräksen välillä ja minkä tyyppiset metallit on yleisimmin käytetty ja niiden ominaisuuksia.